
Wicking-Fin Heat and Mass Exchanger

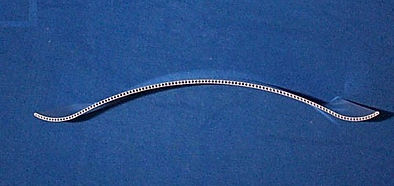

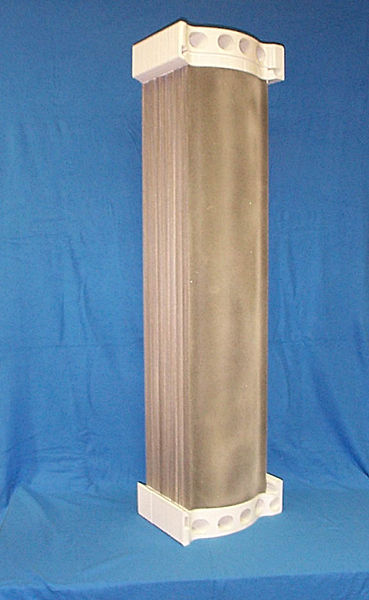
Wicking-Fin Heat and Mass Exchanger
Operating liquid-desiccant heat and mass exchangers (HMX) at low liquid-to-gas ratios is key to suppressing droplet entrainment by the process air. However, an adiabatic HMX (i.e., an HMX with no means to heat or cool the desiccant as it desorbs or absorbs water) must rely on the "thermal inertia" of the desiccant flow to attenuate temperature changes. This "thermal inertia" requirement will lead to flooding rates that are an order of magnitude higher than would be required to keep the desiccant's concentration in a range where high mass transfer rates are sustained.
AILR's first approach to active heat exchange within an HMX was to turn the contact media into a three-fluid heat exchanger. Since many of more common liquid desiccants are corrosive, the plates of the heat exchanger were plastic extrusions with internal passages through which flowed a heat transfer fluid. The first photo at the left shows the cross section of a plastic extrusion that was the plate of a liquid desiccant absorber, the second shows the header for the internal fluid circuit that also delivered desiccant onto the plate, and the third shows an assembled 40-plate liquid-desiccant conditioner.
In work funded under DOE's SBIR program, AILR proved and patented a second design for a liquid-desiccant HMX with internal heat transfer. As shown in the first three figures at the right, this second design inserts layers of contact media—which were first implemented as plastic fins with wicking surfaces, but evolved into pads of corrugated, fiberglass packing—between the rows of an array of metallic heat transfer tubes. In this configuration, the desiccant flowing down on the contact media is periodically cooled (for an absorber) or heated (for a regenerator) as it flow on the surfaces of the embedded tubes.
As described in the SBIR's final report, wicking-fin HMXs can replace conventional finned-tube heat exchangers as the condenser and evaporator of a direct-expansion air conditioner, producing an air conditioner with both a high EER and a low Sensible Heat Ratio for the cooling it supplies. The three-ton liquid-desiccant air conditioner with wicking-fin evaporator and condenser that is shown in the drawing and photo at the right was field tested in 2016 at the Picatinny Arsenal under a grant from the DOD ESTCP program. The final ESTCP report documents the results of the field test.
AILR has field tested liquid-desiccant air conditioners in which the conditioner was a water-cooled HMX and the regenerator was a water-heated HMX. The last photograph on the right is a 6,000-cfm DOAS with paneling removed to show its wicking-fin conditioner. This unit operated successfully with the wicking-fin conditioner rejecting its thermal load via a cooling tower and the wicking-fin regenerator running on hot water provided by a gas-fired water heater.
Finally, a wicking-fin HMX can operate as a frost-free cold coil. In this application, the temperature of the cold coil can be as low -40°C without frost forming on the coil. The coil does condense water vapor from the process air, but instead of freezing the water is absorbed by the flowing desiccant
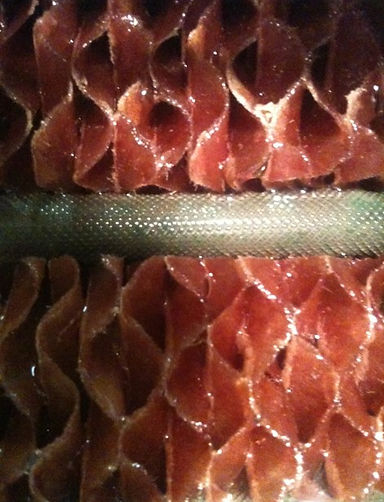

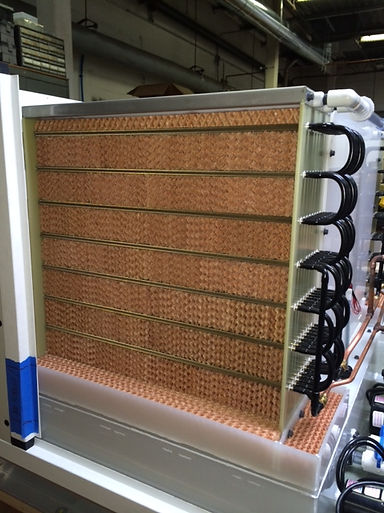


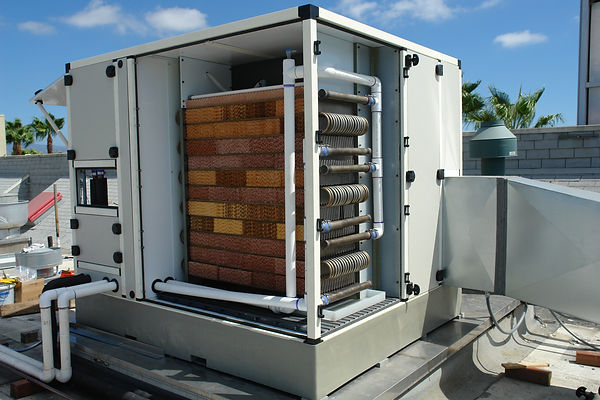